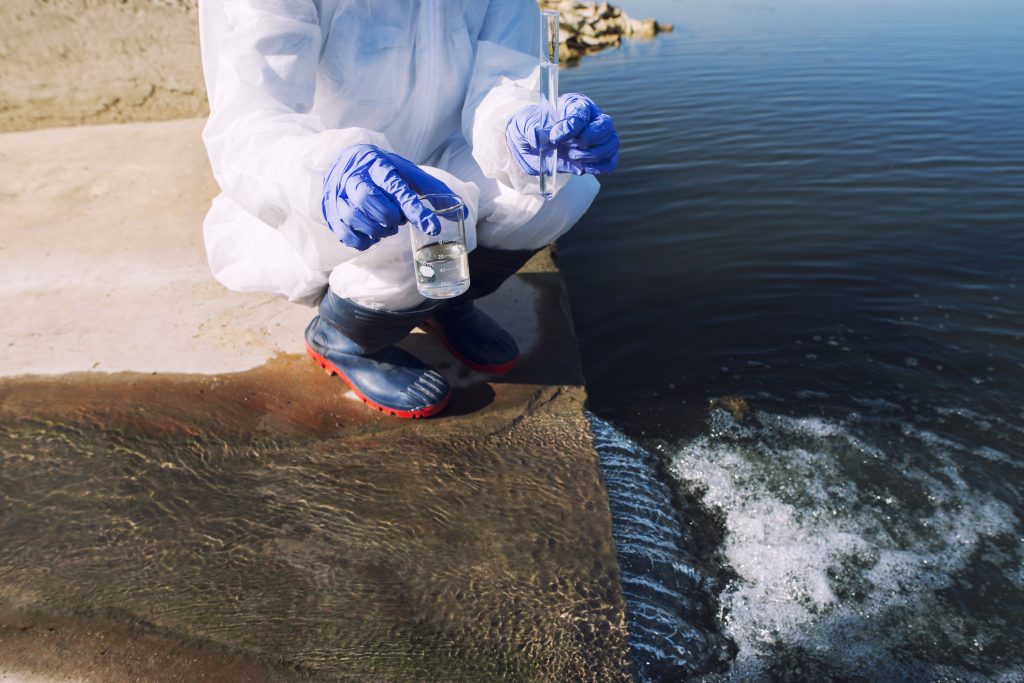
In the evolving landscape of underwater construction and marine engineering, 3D printing—or additive manufacturing—is emerging as a transformative technology, offering the potential to fabricate complex structures directly in submerged environments. As infrastructure projects move further offshore and into greater depths, traditional construction methods face significant challenges in cost, time, logistics, and safety. 3D printing underwater may hold the key to solving many of these issues by enabling on-site, automated, and adaptive fabrication.
This article explores the current state of underwater 3D printing, the technologies driving it, its applications, challenges, and the enormous potential it holds for the future of subsea construction.
1. Why 3D Printing Underwater?
Underwater construction currently involves extensive prefabrication on land, transportation by sea, and complex installation using heavy-lift vessels, divers, and ROVs. These operations are:
- Expensive: Involving costly marine logistics and specialized labor.
- Risky: Subject to unpredictable weather, strong currents, and diver safety constraints.
- Time-consuming: Delays in shipping or weather windows can halt operations for weeks.
Enter 3D Printing:
Additive manufacturing (AM)—printing layer by layer—has the potential to revolutionize this model by:
- Fabricating components directly on the seabed or underwater platforms.
- Customizing structures in real time based on seabed topology or sensor feedback.
- Reducing human involvement in hazardous underwater tasks.
- Accelerating construction schedules by eliminating transportation bottlenecks.
2. How Does 3D Printing Underwater Work?
A. Materials Used
Materials must cure and bond in the presence of water, resist corrosion, and maintain structural integrity under pressure. Common candidates include:
- Hydraulic cements: Special formulations that set and harden in water.
- Geopolymers: Environmentally friendly, chemically resistant, and stable underwater.
- Metal powders: Used in wire-arc or laser-based metal printing, often for small components.
- Polymers and composites: Used for flexible or lightweight subsea parts, coatings, and seals.
B. Printing Techniques
- Robotic Arm Extrusion:
- A robotic arm fitted with an extrusion nozzle deposits layers of concrete or polymer.
- Controlled by real-time software and guided by computer-aided design (CAD) models.
- Used for large structures such as reef modules, protective barriers, and foundations.
- Wire Arc Additive Manufacturing (WAAM):
- Metal wire is melted by an electric arc and deposited in layers.
- Suitable for metallic parts such as brackets, clamps, and repair patches.
- Binder Jetting or Laser Sintering(Experimental underwater applications):
- Involves depositing a binder or using a laser to fuse material grains.
- Currently more viable in dry environments or pressurized chambers.
- Bio-Inspired 3D Printing:
- Mimics coral or shell structures to optimize material use and flow interaction.
- Promotes marine habitat restoration alongside functional construction.
3. Key Applications of Underwater 3D Printing
A. Artificial Reefs and Marine Habitats
- Complex geometries designed to mimic coral reefs can be 3D-printed directly onto the seafloor.
- Materials are chosen to encourage marine biodiversity, offering homes to fish and invertebrates.
- Reduces human impact and boosts ecological restoration.
B. Infrastructure Repair and Reinforcement
- 3D printing allows on-demand patching of damaged pipelines, subsea foundations, and tunnel linings.
- Eliminates the need to lift and replace large components.
- Repairs can be customized to conform precisely to damage geometry.
C. Offshore Renewable Energy Structures
- Bases and anchor points for wind turbines and tidal generators could be fabricated underwater, adapting to uneven seabed profiles.
- Could reduce the need for large foundations and pile-driving operations.
D. Scientific and Military Installations
- Rapid deployment of underwater sensor housings, platform brackets, or temporary habitats for divers or autonomous systems.
- Adaptable in real-time to operational needs and environmental constraints.
4. Advantages of 3D Printing Underwater
Benefit | Explanation |
---|---|
On-site fabrication | Eliminates the need to transport large components, saving time and fuel. |
Adaptive design | Can be modified during printing to respond to seabed conditions or sensor input. |
Reduced environmental footprint | Less dredging, disturbance, and waste compared to conventional methods. |
Increased safety | Minimizes the need for diver-based construction in hazardous environments. |
Scalability and automation | Allows continuous, unattended operations using autonomous robotics. |
5. Technical Challenges and Solutions
A. Material Curing and Bonding
- Challenge: Many traditional materials do not set properly in wet conditions.
- Solution: Develop and optimize underwater-settable concretes, epoxies, and composite blends.
B. Equipment Stability
- Challenge: Maintaining precise control of the printer in currents and low visibility.
- Solution: Use seabed-mounted platforms or tethered robotic arms with real-time stabilization via gyroscopes and sonar.
C. Monitoring and Quality Control
- Challenge: Ensuring accurate layer bonding, material strength, and print alignment underwater.
- Solution: Incorporate sensors, cameras, and ultrasound scanners into the printing unit for real-time QA.
D. Power and Data Connectivity
- Challenge: Supplying reliable energy and control signals to equipment in deep or remote areas.
- Solution: Subsea power umbilicals, wireless acoustic modems, and AUV-deployed battery pods.
6. Future Outlook: What Lies Ahead
Autonomous 3D Printing Systems
Fully autonomous AUVs equipped with additive manufacturing capability could:
- Scout a site.
- Build from scratch or repair as needed.
- Monitor their own output and report data to operators onshore.
Digital Twin Integration
3D printers may be connected to digital twins of underwater assets. As sensors detect damage or erosion, printing systems could deploy to print corrective structures or reinforcements in real-time.
Hybrid Construction Fleets
Combining:
- Underwater printers for complex parts.
- ROVs for fine work.
- AI-controlled drones for logistics and scanning.
Together, they could build entire subsea systems autonomously.
Human Habitats and Undersea Research Stations
Looking ahead, as interest grows in underwater tourism, research, and habitation, 3D printing may allow custom, rapidly assembled habitats—resilient to pressure and tailored to local conditions.
Conclusion
3D printing underwater stands at the crossroads of robotics, material science, marine engineering, and AI. Although still in its infancy, the technology holds enormous promise for building and maintaining subsea infrastructure more efficiently, sustainably, and intelligently than ever before. As challenges in offshore construction mount—with increasing depth, ecological sensitivity, and logistical complexity—underwater additive manufacturing offers a radically new paradigm for creating the next generation of marine infrastructure.
The future of building beneath the waves may not rely on cranes and ships, but on robotic arms and digital blueprints, working silently in the deep.